
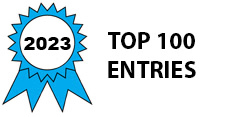
The frequency of droughts has increased by nearly a third globally since 2000. A UN report states that 75% of the world could face drought by 2050, and 5.7 billion people could live in areas with water shortages for a month or more every year. Water scarcity due to climate change alone will necessitate a reduction in leakage.
London was chosen as our location of focus for our project, as it has one of the earliest piped water distribution systems in the world. With more than half of pipes in London over 100 years old and made of corrosion-prone cast iron. This makes London an ideal candidate for our proposed system as it represents a well-developed city where the water leak issues are already the most advanced.
The majority of R&D occurring within the UK’s potable water industry revolves around the detection and location of leaks even though this only accounts for 20% of the repair process’s cost. Most of this cost in repair is associated with the shutting down of busy travel routes. Our product's USP is its non-disruptive nature, meaning that the water companies can negate the need to pay expensive council charges associated with closing roads.
Our market potential diagram displays the market potential for our product in London and the market potential of our product in other countries within Europe.
Our proposed repair process has been described in the attached video and repair process diagram. As the robot travels through the network, it would make use of differential pressure sensors inbuilt into its skin, these pressure sensors will detect discrepancies in the water flow. Using these sensors in parallel with physics-based CFD ml models and Neuromorphic processing units the device would be able to detect exactly where the leak is without the need for visual data.
Our anchoring relies upon soft robotics, utilizing silicone-immersed SMA’s to enact a retreating infill process as displayed in our Repair Application diagram. This allows for fast and controllable actuation without damaging the side walling of the pipes. Following alignment, the robot's secondary anchor begins to expand. Here the SMAs provide heat and pressure for thermally activated resins. This allows for a retreating infill method with cure times between 20 – 30 minutes. This keeps the repair process short minimizing the exposure time of the product to drinking water.
Investigation into the cost of setting up and running the system revealed that for the same leak repair budget that Thames Water currently expends, our proposition could increase fixes by approximately 4.2 times. Meaning, we would be able to catch up and keep pace with new occurring leaks within 8 years of implementation. By comparison, the current Thames Water approach would take around 51 years to reach this same stage. To do this, we would need to implement a fleet of approximately 642 robots. In this theoretical case, we would save Thames water 165 million pounds worth of lost water in the first year alone.
Video
-
Awards
-
2023 Robotics & Automation Category Winner
-
2023 Top 100 Entries
Like this entry?
-
About the Entrant
- Name:Rory Bateman
- Type of entry:teamTeam members:
- Software used for this entry:Blender, Ansys, Comsol, Solidworks, Matlab, Visual studio(python)
- Patent status:none