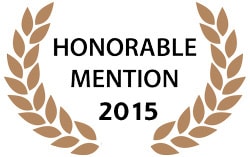
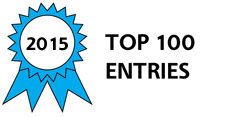
Problem Statement:
According to ARPA-e, in 2013, U.S power plants consumed 38.2 quads of primary energy to generate 12.4 quads of electricity with an average electricity generation efficiency of 33%; 67% of the primary energy was wasted as heat and 2 billion metric tons of CO2 were emitted to the environment. An alternative approach is to use distributed Combined Heat and Power (CHP) systems, in which electricity is generated locally at homes or small businesses by burning Natural Gas in internal combustion engines and exhaust heat is utilized for local heating. 70 million U.S. residential homes could use CHP system if cost could be reduced from current $6,000 per kWe to less than $3,000 per kWe, while simultaneously increasing the efficiency of system from 24% to 40% -- this would save the Nation 5 quads of primary energy and reduce CO2 production by 4%.
Proposed Solution:
LiquidPiston, Inc (LPI), a developer of high efficiency rotary internal combustion engines, proposes to develop a micro Combined Heat and Power (micro-CHP) system running on Natural Gas with ~45% generator efficiency and additional >1kW of usable heat at an estimated cost of $2570 per kWe. If universally adopted, such a solution could reduce CO2 emissions in the US by .5 billion metric tons/yr, reduce costs for electricity generation, reduce loads on the power grid, while taking advantage of plentiful and clean natural gas resources.
Innovation:
The efficiency improvements are grounded in thermodynamics, through integrating: 1) a highly optimized High Efficiency Hybrid Cycle (HEHC) thermodynamic cycle, combining high compression ratio, constant-volume combustion, and over-expansion; 2) internal Water Injection (WI) cooling of thermally insulated engine; water turning to steam builds pressure in the chamber allowing partial recuperation of cooling losses; and 3) heat from exhaust and internal cooling water/steam is recuperated through Bottoming Rankine cycle integral to the base engine.
The thermodynamics is combined with a compact, quiet, low-cost, zero-vibration rotary engine architecture. LPI’s current 70cc X-Mini engine has only 2 moving parts (+Balance of Plant), yet implements a 3-cylinder 4 stroke cycle and fits into a 6”x6”x6” box. In the proposed system, two chambers will fire on NG fuel using the HEHC cycle. The third chamber will be an expander for superheated steam allowing the engine to capitalize on a bottoming Rankine cycle recovering waste heat from the exhaust.
The WI used for internal cooling can be injected at the sealing points of the engine, thereby improving sealing, and possibly eliminating the need for oil lubrication. Without oil, the engine can run hotter, emitting less, and with fewer maintenance requirements.
The developed genset technology will be also used in other fields: range extender for electric vehicles, motorcycles, unmanned aerial vehicles, etc. The technology is scalable to MW size for large installations on ships, etc.
Video
-
Awards
-
2015 Sustainable Technologies Honorable Mention
-
2015 Top 100 Entries
Like this entry?
-
About the Entrant
- Name:Alexander Shkolnik
- Type of entry:teamTeam members:LiquidPiston, Inc.
- Software used for this entry:Solidworks
- Patent status:pending