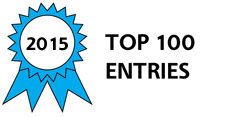
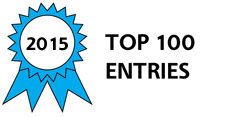
NASA’s Jet Propulsion Laboratory has developed a robot-assisted microsurgery (RAMS) system to allow surgeons to do the impossible and perform surgical procedures beyond the capability of human hand dexterity. A surgeon operating a RAMS system can feel soft tissues with greater sensitivity and can manipulate surgical tools with greater exaggeration and precision. Each joint in the robot arm has a large range of motion, which reduces the chance of a joint reaching a limit during operation, and little to no static friction, which means that small, incremental movements can be made without overshooting. In addition to its usefulness during microsurgical procedures of all kinds, JPL’s RAMS system can be used a simulator to train for these procedures.
THE TECHNOLOGY
JPL’s RAMS system is comprised of four subsystems: mechanical, electronics, servo control and high-level software, and user interface. The mechanical subsystem includes a master input device handle with pushbutton switches for opening and closing the microforceps on the slave robot arm. This arm has six degrees of freedom, measures 2.5 cm in diameter, and includes four mechanically-decoupled joints to provide partial functionality, even with one joint failure. The tip of the robot arm allows for simultaneous sensing of force interactions and manipulation with the microforceps. Measured force interactions are amplified, processed by the electronics and software subsystems, and used to drive the master control device. Similarly, six arm and wrist motors provide force feedback on the torso, shoulder, elbow, and wrist axes. A RAMS system has been implemented using dual drive-trains that were pre-loaded relative to one another to minimize backlash. Precision ball bearings were incorporated in every rotating location to minimize static friction. This RAMS system was successfully used to remove a 0.015 inch diameter particle from a simulated eyeball.
BENEFITS
* Microsurgical manipulator can scale down hand motions to less than 10 ?m
* Amplified forces allow surgeons to feel soft tissues with greater sensitivity
* The six degrees-of-freedom arm is capable of very precise relative positioning
* The robot-assisted microsurgery system is compact and lightweight
ILLUSTRATIONS
FIGURE 1 – The slave robot arm includes a torso joint 204, a shoulder joint 206, an elbow joint 208, and a wrist joint 210. A tip 220 of the arm allows for simultaneous sensing of force interactions and manipulation with the microforceps.
FIGURE 2 – The master control device includes a base 110 that houses high resolution optical encoders for position sensing, torso 402, shoulder 404, elbow
406, wrist 408, and six-axis force sensor 410 for force feedback. A handle 412
has pushbuttons that allow the operator to open and close the microforceps on
the slave robot.
PUBLICATIONS
US Patent 6,233,504
-
Awards
-
2015 Top 100 Entries
-
2015 Top 100 Entries
Like this entry?
-
About the Entrant
- Name:Hari Das
- Type of entry:teamTeam members:Hari Das, Tim Ohm, Curtis Boswell, Robert Steele
- Patent status:patented