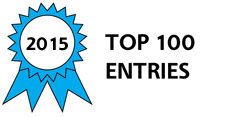
Transformers are used throughout the world as a means of changing the AC supply voltage. However these are imperfect solutions as they have substantial no-load losses, are less efficient at both high and low loads, have significant regulation with load (and the line out follows input line changes), poor output limitation against overloading and are large and heavy using much iron and expensive copper. An alternative method has been developed using high frequency switching techniques, which is extremely compact, lightweight and highly efficient. It provides a user-settable closely regulated output voltage with current limit, and can reduce or increase the supply voltage, or both. Ideal for general purpose protected autotransformers and voltage optimisation as well as instrumentation/lighting/heating/motor supplies at very high efficiency.
The technique shown in the schematics is deceptively simple and similar to conventional buck and boost DC converters but utilises pulse-width modulated AC switches. (Previous attempts to achieve transformers such as this were severely limited to a few hundred watts at low efficiency and high waveform distortion.) The inputs and outputs require filtering to prevent harmonics and interference on line and outputs. These filters are inductive and capacitive; the requirement for inductive storage means that switch timing must be extremely precise (of the order of a few nanoseconds), as without lossy ‘snubbing’ of the transients inherent in switching inductors, miss-timing would cause overvoltage and either high losses or subsequent failure of the switches. To maintain high efficiency switching has to be done extremely quickly but without switch cross-conduction causing shoot-through current and again high losses or switch failure. Ultra-fast switching at high current also causes high dV/dT across these switches, potentially exceeding the switch withstand capability, and this will result in loss of control and/or instantaneous failure of the switches (and of the driver circuitry).
Recent advances in semiconductor technology such as silicon MOSFETs with inherently fast body diodes, or Silicon Carbide/Gallium Nitride devices make it possible to achieve extremely high dV/dT withstanding capabilities for the switches (and also for the essential isolated driver devices), leading to power capabilities in excess of 5KVA, at efficiencies of 99%, no load losses of around 3W and harmonic distortion less than 0.3%. A 5KVA module is around 25x10x10cm and weighs around 1.5Kg. It is protected against overcurrent and an unlimited number of modules can be run in parallel so that much higher outputs can be provided. The cost of such a module will be 360W, efficiency 95%, cost $9000, versus 12× 5kW paralleled modules, fully regulated, current limited, no load power 36W, efficiency 99%, cost $1200. Saving >330kWh per annum.
-
Awards
-
2015 Top 100 Entries
Like this entry?
-
About the Entrant
- Name:Alistair Macfarlane
- Type of entry:individual
- Software used for this entry:Spectrum Microcap 11
- Patent status:pending