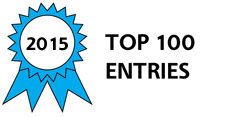
Referencing Astro2010: The Astronomy and Astrophysics Decadal Survey and 2012 National Research Council report entitled “NASA Space Technology Roadmaps and Priorities: Restoring NASA’s Technological Edge and Paving the Way for a New Era in Space”3, there is a need for large aperture, lightweight mirrors for future UV/Optical telescopes. The cost of current normal incidence space optics is from $4-6 million per square meter of area per Dr. Phil Stahl (NASA SBIR Topic S2.03, 2012). Trex T300HoneySiC is a new zero coefficient of thermal expansion (CTE) ceramic matrix composite (CMC) material made by an additive manufacturing (AM) process which has demonstrated feasibility (Technology Readiness Levels 1-5 achieved via Phase I and Phase II SBIR) for ultra-low areal cost, and ultra-low areal density (5.86 kg/m2) mirror substrates and opto-mechanical structures. T300HoneySiC panels have a density that is 1/5 the value of beryllium and a net production cost of $38K per square meter (unpolished), less than half of NASA’s goal of $100K per square meter!
T300HoneySiC mirror substrates and opto-mechanical structures are made in several steps:
1.) Mold and cure a prepreg consisting of T300 carbon fabric and a pre-ceramic polymer . The desired ply layup for plain weave fabric is a quasi-isotropic layup;
2.) Additively form complex structures (optical benches, mirror substrates, struts, etc.) using pre-ceramic polymer as an adhesive to join as-cured laminate facesheets and honeycomb cores. Any machining that is required is done at this stage of the process;
3.) Convert the cured assembly to dense, monolithic CMC via polymer-infiltration-pyrolysis (PIP) using preceramic polymer.
Once converted to ceramic, these structures are ultra-lightweight, stiff, and dimensionally stable as proven by the material properties measured by Southern Research Institute.
The AM process eliminates machining associated with lightweighting, reducing cost, schedule, and manufacturing risk. With all manufacturing assets in a single location, our process would allow telescope parts to be made in as little as 3-weeks’ time. Notable, T300 is used in the Boeing 787 Dreamliner, while PIP is the process for making large solid rocket motors, thus the feasibility of scaling is apparent. Our AM process makes T300HoneySiC a material that is rapidly maturable to high Technology Readiness and Engineering Readiness levels.
It is not a far-fetched idea that this breakthrough and game changing material will lead to the restoration of NASA’s Technological Edge with respect to the large monolithic mirror capability that has been witnessed in China (4-meter monolithic silicon carbide with silicon cladding) and France (3.5-meter monolithic Herschel silicon carbide telescope). With maturation of T300HoneySiC, NASA will be able to manufacture large UV and UVOIR mirrors that are lighter, less expensive and dramatically faster than any other technology in any country on the planet. T300HoneySiC has the potential to be the disruptive technology for all beryllium, ULE® and Zerodur® large optics.
-
Awards
-
2015 Top 100 Entries
Like this entry?
-
About the Entrant
- Name:Bill Goodman
- Type of entry:individual
- Software used for this entry:ProEngineer
- Patent status:pending