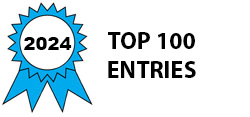
Challenge - Making orbit is always a challenge of converting chemical energy into kinetic energy. Doing that in one stage means you must deal with a wide variety of flight conditions with one solution, but it also means that there is no integration needed before the rocket launches. It also means that there is no reason the rocket could not land and fly again like an aircraft. This challenge of getting all the engineering trades-offs to balance-out into something useful has been the goal of several unsuccessful efforts over the years.
Our Approach - TGV Rockets has leveraged advances in both technology and materials and has gone back to the drawing board to create a “fresh-sheet” design for a practical REUSABLE Single Stage to Orbit (SSTO) rocket. TGV began by creating an SSTO designed to be moved by ordinary road transportation. When combined with our new engine class, this ultimately yielded a conceptual SSTO capable of putting one ton into LEO. A single stage means there is no integration and a vehicle is ready to fly right from the factory, just like normal aircraft.
Our design for an SSTO reusable launch vehicle (RLV) is based on using an aerospike and TGV’s eutectic fuel blend propulsion technologies. We began with the design of an existing fully expendable small launcher and added modern propulsion technology to leverage using the 1950’s balloon structure. The result is a practical reusable SSTO with an altitude compensating engine merged with TGV’s proprietary tri-propellant eutectic fuel blend technology. Eutectic-blend fuel offers the prospect of 6-7% lighter structural mass fractions in launch vehicles while still offering excellent performance.
Our small SSTO receives significant benefit from tri-propellant engines. Altitude compensation reduces performance loss during landing. Common wall bulkheads provide significant dry mass reduction and increased packing factors. Tri-propellant fuel combination reduced dry mass, engine mass and gross lift-off weight (GLOW). A nominal payload of 2000 lb. to LEO was achievable at a 74-ton GLOW.
As we have designed our SSTO for Vertical Lift-Off, so too have we designed it for Vertical Landing on return. With deep throttling capability, our ElectroCycleTM engine allows for a smooth, guided and safe return to the launcher’s point of departure.
Once returned to base, the launcher will be inspected to ensure there has been no damage and consumables will be replenished. At this point the vehicle will await a new payload for integration and eventual re-launch. We have designed our SSTO to require a minimal ground crew and only the most basic ground support equipment. Our system concept frees the rocket from existing launch complexes like Cape Canaveral as it can be launched from and returned to minimally equipped sites accessible by road.
Our target mission rate for year one will be 12 flights increasing as we gain more experience.
Video
-
Awards
-
2024 Top 100 Entries
Like this entry?
-
About the Entrant
- Name:Chuck Burch
- Type of entry:teamTeam members:
- Pat Bahn
- Patent status:pending