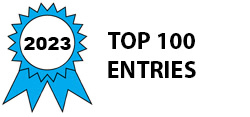
We bring fundamental changes to both the core Heat Pump physical implementation and industrial systems-level application to fully enable Industrial Process Heat Decarbonization immediately/”piloted” to 230°C/445°F, mid-term to 390°C/740°F, and longer-term to at least 600°C/1100°F. Our target industrial applications include all General Process Heat, Food and Beverage (piloted), Pulp and other Drying, Plywood/Wood-Products Curing, and Materials Pre-heat for higher temperature processes.
The root of this innovation set is both a specific disruptive step for electric heat pump/refrigerant equipment itself, but also new approaches to process heat energy recovery, reuse a.k.a."Energy Recycling", and efficient distribution to eliminate at least 80% (COP=5) and up to 89% (COP=9) of the Source Energy required, with over COP=9 source energy efficiencies using added Clean Energy such as Concentrating Solar Thermal or available waste heat (both piloted). To enable rapid rollout of this breakthrough, we are already developing the essential Thermal Process Analysis and Transformation Visualization and Planning tools for management and engineers to gain rapid comfort with the concepts and ensuring Rapid Climate Action. The approach will also Store Thermal Energy at a Levelized Cost of Storage (LCOS) 70% below electric battery cost goals for maximal process efficiency and minimized costs via time-shifting energy for maximal Renewable Energy utilization. The result will be the lowest cost Industrial Process Heat Decarbonization possible ... at least through 600°C/1100°F. We have received interest from multiple industries including food and beverage, wood products drying, and fabric dying.
Part of our core technology is "Modular and Fully Encapsulated Heat Pumps" and associated servicing tools/techniques which bring certified outer encapsulation of all refrigerant elements to eliminate all possible refrigerant leakage. This allows use of any refrigerant in a heat pump system and provides more cost-effective and higher quality "depot" servicing whether on-site or off-site. Refrigerant leakage at high temperature is the single largest barrier to High Temp Heat Pumps (HTHP) -- a barrier we eliminate by design. Our encapsulated heat pumps will eventually include multiple thermal transfer configurations such as direct-to-air, via water or benign refrigerant transfer, or via thermal "plates", all using double-wall heat exchangers to ensure any leakage is fully contained. Modularity with full digital monitoring, hot-swapping, and on-site spare ensures process continuity and the lowest possible cost equipment servicing.
Once the possibility of leakage is removed from a heat pump system, the Pressure-Temperature graph included (truncated at Heptane) shows how various long proven refrigerants and hydrocarbons can be used for multi-stage Heat Pump output well past 230°C/450°F, even with pressures limited to ~40 to 375 PSI -- pressures efficiently achieved with Scroll Compressors (between horizontal Red lines). One such multi-stage refrigerant path to 230°C/450°F (the temperature a large multi-national has requested for "drying" piloting) would be R-410a/R-32 to R-290 Propane to R-600 Butane to R-601 Pentane to Heptane, all very common and there are multiple other refrigerant selections possible. The Green arrows (labeled "X") show how the heat output from one stage becomes the input to the next with ~6°C/10°F overlap to account for heat exchanger ΔT’s.
Video
-
Awards
-
2023 Top 100 Entries
Like this entry?
-
About the Entrant
- Name:Rick Clemenzi
- Type of entry:teamTeam members:
- Patent status:pending