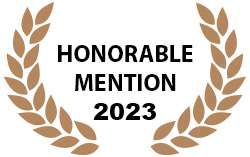
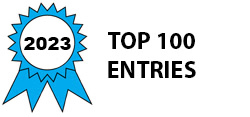
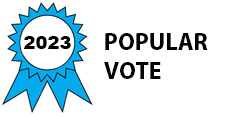
Development of the world's first carbon fiber reinforced thermoplastic (CFRTP) composites door marks a pioneering achievement in the field of automotive manufacturing and composite materials. The ultra-lightweight CFRTP door structure, developed as a lightweight alternative for the closures of the 2016 Acura MDX, is not only 45 % lighter than its equivalent baseline steel door structure, but also significantly easier to manufacture and assemble. Use of CFRTP composites allowed further structural optimization, and significant parts consolidation, reducing the number of structural parts to be manufactured and assembled by half (52 %).
This ground-breaking initiative, sponsored by the Department of Energy and Honda Development and Manufacturing of America, LLC, sought to reduce the weight of automotive doors by an ambitious 42.5% in a cost-effective manner, without compromising crash performance, durability, fit, or function. The cost increment was capped at $5 per pound of weight reduced, and the proposed design and manufacturing methodology would have to meet an annual production volume of 20,000 units. An essential aspect of this endeavor was the self-imposed goal of developing a sustainable design that ensures 100% recyclability.
A systems engineering approach was employed, leveraging part consolidation and modern structural optimization tools, to develop a design that utilized reprocessable Nylon-based-woven continuous carbon fiber laminates that were readily thermoformed, similar to hot forming of sheet metal. Thus, the design could be realized without significant modification to the sheet metal forming equipment, signifying an innovative and cost-effective use of existing infrastructure. Finite Element Analysis (FEA) based optimization strategies enabled 17 structural steel parts to be replaced with just two lightweight CFRTP panels, and a few local steel and aluminum sheet-metal parts for locally improved strength and toughness.
The manufacturing process significantly affects the microstructure of the CFRTP component, owing to its anisotropic nature. Manufacturing process parameters affect microscopic properties such as, fiber orientation, voids and residual stresses. These, in turn, determined macroscopic mechanical properties such as part-warpage, stiffness, strength and toughness. Thus, a novel manufacturing-to-response (MTR) pathway was conceived to systematically understand the effects of manufacturing process parameters at different length scales and develop predictive models to accurately determine micro- and macro-mechanical properties. Comprised of multiple material characterization, finite element simulations, and experimental validation loops at different length scales, this pathway enabled prediction of thermoforming process effects and enhance the scientific understanding of thermoforming of fiber reinforced thermoplastics.
Improved FEA simulations, that also captured the predicted thermoforming process effects, helped refine the CFRTP door design. The MTR pathway ensured that the manufactured CFRTP door prototype not only met the federal crash safety standards (FMVSS 214, IIHS moving deformable barrier), but also exceeded the crash performance of the baseline steel door by a notable margin. This holds substantial implications for the U.S. economy and the future of sustainable transportation through improvements in fuel efficiency and reduction in vehicle emissions. This innovative CFRTP composite door demonstrates the potential of thermoplastic composites, their strategic use, and development of progressive manufacturing techniques to ultimately open new doors for composite materials for automotive applications.
-
Awards
-
2023 Manufacturing & Materials Honorable Mention
-
2023 Top 100 Entries
-
2023 Top 10 Most Popular
Like this entry?
-
About the Entrant
- Name:Sai Aditya Pradeep
- Type of entry:teamTeam members:
- Amit Deshpande
- Madhura Limaye
- Anmol Kothari
- Aditya Yerra
- Lukas Fuessel
- Pal Swaminathan
- Ryan Hahnlen
- Duane Detwiler
- Shridhar Yarlagadda
- Gang Li
- Dr.Srikanth Pilla
- Patent status:none