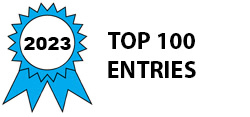
Most of the world’s power is generated at centralized locations (power plants, wind or solar farms, etc.) and then must be transmitted over cables at high voltage (HV) to minimize electrical losses. The predominant modern cable designs for high voltage undersea and underground power cable utilize high performance polyethylene insulation that is crosslinked to raise the operating temperature and enable emergency and short circuit overload temperature protection. Such HV insulation compounds are relatively sophisticated products, requiring ultra clean manufacturing materials and conditions, including packaging in a clean room environment to avoid external contaminants that can cause electrical breakdown under HV stress.
The polyethylene additives that are incorporated to induce crosslinking produce byproducts, including methane. Therefore, such cables must be degassed at 60 – 70°C for up to a month before cable manufacturing can be completed and the cable can be tested and shipped.
DOW ENDURANCE(TM) HFDD-4201 Compound for Cable Systems is a fully formulated polyethylene compound, supplied by Dow as pellets that are melt extruded by cable manufacturers to make the insulation for critical underground and undersea HV cable applications up to 500 kilovolts (500,000 volts), providing breakthrough reliability, manufacturing efficiency and sustainability.
These breakthroughs are achieved via a combination of polyethylene molecular architecture and patented additive technology to enable higher crosslinking efficiency, resulting in lower byproduct levels. Additionally, the new technology enables reduced premature crosslinking (scorch) during insulation extrusion, thus providing higher manufacturing efficiency via longer production run lengths.
The result is >70% reduction in crosslinking byproduct levels, including methane, and 60% improvement in resistance to scorch versus incumbent insulation compounds. This effectively allows for complete elimination of the degassing process by cable manufacturers, enabling inventory and energy cost savings and reducing byproduct chemical waste and emissions. In addition, the longer run lengths enabled by higher scorch resistance reduce the frequency of costly manufacturing line shutdowns and cleanouts, significantly reducing material scrap. This allows up to 20% lead time improvement for cable manufacturers and generates cost savings of 3000-7000 USD/km of cable (depending on the cable design). The savings come from reduced startup (200-300 USD/km of cable), material savings (2000-5000 USD/km of cable), inventory savings (100-400 USD/km cable) and energy savings (150-300 UDS/km of cable). The reduced degassing energy consumption and reduced methane emissions from the cable also contribute to CO2 footprint reduction from cable processing. This is achieved without sacrificing the other critical and challenging properties required for high voltage insulation, including crosslinking rate and dielectric properties.
Manufacturing entails production of polyethylene followed by a melt compounding operation to incorporate the additives. Feasibility of manufacturing has already been established via multiple full scale commercial production runs, and the product is now being sold commercially. The market for the product is well established, with multiple global cable producers having already completed full scale qualifications. Quick market penetration is expected for DOW ENDURANCE(TM) HFDD-4201, since its predecessor enjoys large volume commercial sales and DOW ENDURANCE(TM) HFDD-4201 meets all the stringent requirements of its predecessor while also providing the above-mentioned improvements.
Video
-
Awards
-
2023 Top 100 Entries
Like this entry?
-
About the Entrant
- Name:Jeffrey Cogen
- Type of entry:teamTeam members:
- Roshan Aarons
- Edit Berczi
- Randall Cuntala
- Caroline Grand
- Tim Person
- Michael Petr
- Robert Scheid
- Saurav Sengupta
- Yabin Sun
- Kainan Zhang