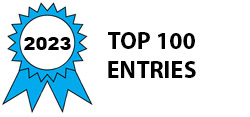
Multiphase electric machines possess several advantages when used in the electric drive system for automotive, aerospace/defense, rail, marine, and manufacturing industries. The performance of an electric drive system in extreme working conditions is extremely compromised. An electric drive suffers from torque derating, a decrease in efficiency, and an increase in loss of lifetime (aging) as its parameters change due to the change in operating and ambient temperatures.
To address the crucial issue of electric machine performance degradation due to the harsh environment and operating conditions a design has been developed based on the dynamic drive control (provisional patent filed). The dynamic drive control scheme facilitates the control of multiphase electric machines to overcome the problem of thermally derated torque, minimizing the loss of lifetime (aging), and improving the energy conversion efficiency of the multiphase electric machine. A dynamic control scheme allows the controller to schedule (re-compute) itself based on the changes observed in the parameters of the electric drive system to address the issue of thermally derated torque. It utilizes the machine’s losses to compute the optimal flux demand to ensure improvements in the energy conversion efficiency of the machine and develop a dynamic relationship between road load demands and flux. The optimal cost function is formulated based on the operating voltages and currents’ constraints to minimize aging.
This proposal is composed of a systematic application of knowledge toward the design, development, and hardware realization of the prototype. The focus will be on the needs of the industries as follows: (1) efficiency improvements of approximately 2%, (2) minimizing the aging by approximately 2.01%, and (3) meeting the road load demand with the Root Mean Square Error (RMSE) of 0.195 with the variations in operating and ambient temperature.
-
Awards
-
2023 Top 100 Entries
Like this entry?
-
About the Entrant
- Name:Ahmad Hussain Safder
- Type of entry:teamTeam members:
- Patent status:none