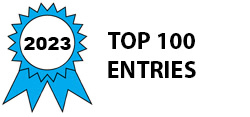
TokaTrac CVT was developed using well established design principles to produce a CVT that can be designed according to specific torque, durability and duty cycle requirements. Our patent pending* CVT technology enables features such as:
* Full CVT capability under all load conditions i.e. max. input torque across all ratios
* Geared regeneration, bidirectional i.e. motor can be placed on either side
* 91-94% efficiency, performance (MATLAB Simscape simulation)
* Highly configurable; optimize for application e.g. 374%, 510% ratio
* Shaft driven, fully enclosed system; practically zero maintenance
* Simple, durable, lightweight design (2.3kg without external casing)
* Highly responsive, fully automated ratio control
TokaTrac CVT creates a traction drive by utilizing a thin film of an elastohydrodynamic lubricant (EHL). EHL is a high viscosity lubricant that ‘solidifies’ momentarily under high contact pressure between two hardened metal surfaces, thus providing a traction force.
TokaTrac CVT scaling:
~~~~~~~~~~~~~~~~~~~
9.2 kW (current ebike CVT design):
* Max. input torque depends on the duty cycle; for an ebike application, it’s about 55 N.m.
* Whereas, it’s about 26 N.m for a scooter application with an ICE or electric motor running at 3,500 rpm.
* Power (Watt) = 0.105 (coefficient of friction established by traction fluid) x N.m x rpm, therefore, this will result in low Hertzian contact stresses of around 1.35 GPa. Thus, the CVT can be manufactured using relatively low cost 655M13 (EN 36B) steel (case hardened to 60 HRC) *
15.8 kW:
As per above example but at 6,000 rpm input, will result in 15.8kW
34.6 kW:
As per the first example, but using steel such as KUJ7 low cost bearing steel by Koyo, which can handle 2.7 GPa (55 Nm) at a high duty cycle, for the disk and rollers. This will result in 20.2 kW at 3,500 rpm and 34.6 kW at 6,000 rpm.
And beyond by further varying input torque, RPM and design & space relationships.
Applications for modern traction drives are diverse:
~~~~~~~~~~~~~~~~~~~~~~~~~~~~~~~~~~~~~~~~~~~~~~
Automotive transmissions – both EV and ICE:
* e-Axle differential for LEVs, 3 & 4-wheelers
* motorcycle scooters, mopeds - an efficient alternative to rubber-belt CVT (≤ 50% losses)
* powersports, snowbikes, snowmobiles, ATVs, and recreation vehicles e.g. golf carts
* Marine propulsion; outboard drives (ICE/EV) – higher torque and better acceleration at lower prop RPM
* Drone propeller drives e.g. heavy lift unmanned aerial systems (UAS), including unmanned compound helicopters
* Subsea - drones; Remotely Operated Vehicles (ROVs), tooling et al
* Hydrostatic transmission alternative e.g. turf care, lawn mowers
* Variable Speed Drive (VSD) alternative e.g. for pumps, compressors etc.
* Small WTG (wind turbine generators) - eliminate the need to adapt the frequency to the grid & maximise the energy yield.
* Household appliances e.g. dryer/washing machine due to broad power range parameters
* AgriTech, Power take-off
* Aircraft power - CVT integrated power generator
* Textile machinery, industrial motion, conveyors, e-hoist/winch
* Turbocharger - turbine driven using engine exhaust gas flow
* Air-conditioning systems
* Zero emission drive systems
* Geared motor drives
Currently prototyping.
Video
-
Awards
-
2023 Top 100 Entries
Like this entry?
-
About the Entrant
- Name:Bruce Thompson
- Type of entry:individual
- Patent status:pending