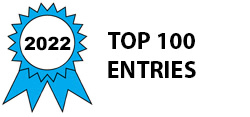
Currently, about three billion people still cook with traditional methods such as a three stone fire. This method of cooking causes all sorts of issues ranging from deforestation to exposure to toxic smoke. Clean cookstoves are a solution, however, they are largely inaccessible to people who need them most. Fortunately, carbon credits are making local production of cookstoves in LMICs economically viable.
One of the biggest barriers in local production is processing the sheet metal used to make the stoves because there is no current machine that meets the needs of thriving in a resource limited setting such as being hand-powered, easily repaired, and cost effective for a mid level production volume. The closest piece of equipment is a foot powered table shear, however, the current back gauge system for these machines is not compatible with the thin sheet metal needed for clean cookstoves.
As a result, the team at BDL developed a custom back gauge which is full compatible with a current table shear. The back gauge will improve the production process of the factory by allowing them to transition from marking sheet metal and cutting with hand shears to simply setting the stop to the desired depth of cut and processing entire rolls of sheet metal. The core approach of this project was the Human-Centered Design process which allowed the team to analyze the problem from the perspective of the end user. This resulted in design decisions such as designing each part so that it could be manufactured by a machine shop that might not have access to CNC machines. It is also worth noting that the Back Gauge shown in the video has been tested and will be sent to a cookstove factory in Lira, Uganda later this year.
While this invention was designed for the production process of cookstoves, it can easily be applied to any factory around the world in a resource limited setting that can only invest low-capital machinery for a mid-level production volume.
Video
-
Awards
-
2022 Top 100 Entries
Like this entry?
-
About the Entrant
- Name:Emilio Taltique
- Type of entry:teamTeam members:Emilio Taltique, Bryan Willman
- Software used for this entry:SolidWorks
- Patent status:none