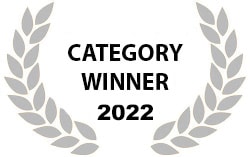
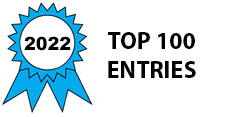
The 3D printing industry has grown quickly over the last decade with average compound annual growth rates of around 27% leading to a market size of $17.7 billion in 2022. The use of 3D printing for large-scale polymer objects is also a high growth area, but is constrained by technical issues that arise when printers are scaled up to extrude higher volumes from large diameter nozzles. Not only do material costs increase dramatically, but materials issues such as contraction, warping and cracking increase. Printing issues such as long cooling times, sagging, bridging and supports also become much more problematic.
In nature you often find tubular structures where high strength to weight ratios and efficient material use are required. Our pioneering tube 3D printing process uses the same idea to print large strong parts with minimal materials and no assembly required. Tubes cool much faster than solid rods, so it is possible to print in free air without supports! Our case studies have shown material reductions over 60% are possible. With our novel extruder design it is also possible to print tubes at 90 degrees from the nozzle axis. This means the tubular structures can be printed using conventional 3D printing software and simple cartesian 3D printers. Printing with tubes also means fillers are not required to reduce material costs and thermal issues. This means the printed objects are much easier to recycle if needed. It may also be possible to print with challenging single use semi-crystalline polymers such as HDPE and PET, saving them from landfill. The tubes can easily be sealed to create airtight chambers. Perfect if buoyancy is desirable. The surface of the tubes can be filled and coated to improve appearance and strength.
Applications for the 3D tube printing process are extremely broad, depending on the polymers used and the geometry of the tubes. Examples include watercraft, furniture, tooling forms, lighting products, vases, the possibilities are endless.
For more information see our paper published in the Additive Manufacturing journal.
https://doi.org/10.1016/j.addma.2020.101606
Video
-
Awards
-
2022 Manufacturing/Robotics/Automation Category Winner
-
2022 Top 100 Entries
Like this entry?
-
About the Entrant
- Name:Hadley Brooks
- Type of entry:teamTeam members:Nick Hopkins, Ruben Janse van Vuuren.
- Software used for this entry:Solidworks
- Patent status:none