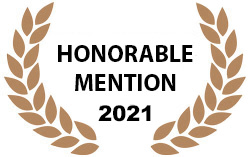
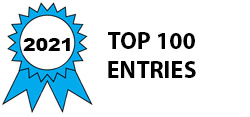
The application of additive manufacturing has allowed a research team at The University of Bath (UK) to significantly improve the achievable performance of SiC and other wide band gap semiconductor devices, allowing an increase in inverter performance that will improve the efficiency, packaging and energy density of electric vehicle powertrains across all transport sectors.
The performance of inverters has a significant impact on how hard you can drive many components of an electric vehicle powertrain. The use of wide band gap semiconductors significantly improves this performance, but these devices are costly and system designers are often unable to take full advantage of their potential because of practical difficulties managing both thermal loads and Electro Magnetic Interference (EMI).
In a majority of inverters, cooling is the job of a thick aluminium heat sink (cold plate) that is usually liquid cooled. The efficiency, reliability and performance of SiC switches falls significantly as temperature rises, so the ability of this plate to extract heat from the inverter is critical.
A conventional cold plate is a slab of aluminium into which cooling channels are machined. Because of process limitations, it has so far been impossible to use intricate shapes or to specify thin walls between the channels. By designing a plate with a complex lattice internal structure built from walls less than 1 mm thick, the Bath team has created a more efficient design that will allow the power electronics to carry up to ten percent more current.
To deliver affordability at scale, the manufacturing solution will be to 3D print the complex shapes and insert them into a conventionally manufactured aluminium cold plate. The Bath technique only employs the more expensive manufacturing technique where it adds the most value.
Additive manufacturing has also been employed to more effectively manage EMI, which is created not only by a high switching frequency, but also by the rate of change of voltage in the transition from conducting to not-conducting. The impact of EMI is made significantly worse when the distance between switches and the gate drivers, as well as the area of the connection, is large, because even this small inductance leads to damped-resonant ringing of the switches as they transition. The conventional solution is to specify switching speeds that are lower than the capability of the SiC (or other high band gap) device, compromising system performance.
Additive manufacturing allows the Bath team to manufacture the connections with highly optimised 3D geometries. This allows a new design in which the gate drivers are closer to the switches, reducing the loop inductance that can limit the achievable switch performance. The resulting reduction in switching losses translates to both an increase in converter efficiency, especially at low loads, and an increase in inverter power without upgrading the cooling system (or a simplified cooling system for the same power).
The focussed application of additive manufacturing is therefore allowing the Bath team to design inverters that initiate a virtuous circle of efficiency improvement within the electric vehicle powertrain.
-
Awards
-
2021 Automotive/Transportation Honorable Mention
-
2021 Top 100 Entries
Like this entry?
-
About the Entrant
- Name:Richard Gotch
- Type of entry:teamTeam members:Professor Peter Wilson, Mr Oliver Holt and colleagues at The University of Bath's Institute for Advanced Automotive Propulsion Systems
- Software used for this entry:Various for concepting, design and simulation / optimisation
- Patent status:none