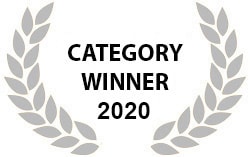

Technological developments are moving ever faster in our modern society, and so are the pressure put on industries to produce safe and sustainable products within a circular economy perspective. Hybrid assemblies, joints of dissimilar materials, are key in modern product design and found everywhere - in your smartphone, car, TV, dishwasher, in planes and so on. However, in modern products we increasingly rely on engineering plastics and fiber-reinforced plastic composites, which is intrinsically hard to bond to other types of material - and using industrial glue you cannot easily recycle the plastic part.
This becomes particularly challenging for the transportation sector with especially stringent legislations. New lightweight materials are the only solution to meet these legislations, by making vehicles much more fuel-efficient and less polluting. Engineering plastics and fibre-reinforced plastic composites (the latter is stronger than steel but 70% lighter) are considered key for lightweight materials to reduce future’s vehicles weight. However, there is a huge downside that limits implementation: Lack of cost-efficient, strong and sustainable joining technologies to combine these materials.
To solve this challenge, RadiSurf has developed and patented the groundbreaking RadiBond technology, based on nanometer-thin coatings of polymer brushes, that provide ultra-strong and ultra-tight bonding between metals and the challenging plastic or plastic composites typically used for automotive and aerospace. RadiBond is a sustainable bonding technology that can also easily be reversed at product end-of-life for disassembly and recycling of the bonded parts.
Polymer brushes are essentially plastic chains, chemically tethered onto a surface that can be applied onto almost any inorganic material and certain plastics. The polymer brush layer make incompatible surfaces compatible, meaning that e. g. a coated metal surface can as easily be joined to a plastic as the plastic can be joined to itself. This happens because the polymer brushes blend into the structure of a plastic to create a form of bonding called chemical entanglement. Chemical entanglement can be visualized as a an immensely tight nano-velcro bonding between the polymer chains of the plastic and the polymer brushes.
The assembly between a coated polymer brush surface and a plastic or fiber reinforced plastic composite is achieved by melting the plastic in the interface, typically by welding or molding. The bonding can again as easily be reversed by remelting the plastic in the interface to break the chemical entanglement bond and get clean parts that can be recycled or reused.
The process for applying the RadiBond polymer brush layer is a fast, simple and cost-efficient dipping process, taking down to five minutes that can easily be applied on both complicated geometries and large areas. However, application by spray and paint-on are
also under development. The application cost is similar to typical industrial adhesives, but with a superior performance - offering cohesive fracture (the plastic breaks) for metal assemblies to even-high performance plastics and plastic composites such as PEEK, PPS, PC and PVDF.
The business potential of RadiBond is immense, and it will be ready for market within the next 6 months.
-
Awards
-
2020 Manufacturing/Robotics/Automation Category Winner
-
2020 Top 100 Entries
Like this entry?
-
About the Entrant
- Name:Espen Hvidsten Dahl
- Type of entry:teamTeam members:Espen Hvidsten Dahl, Mikkel Kongsfelt
- Software used for this entry:None
- Patent status:patented