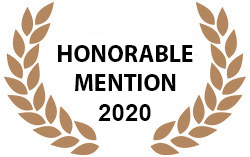
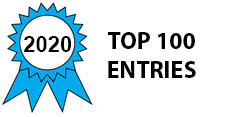
Provide an e-vehicle conversion kit using my patented (US Patent 9,124,144 B2) dual radial gap, high-power density, low RPM DC electric motor in a direct drive application to convert conventional IC powered vehicles to full electric power. These kits can be configured to provide direct drive power to any front or rear drive vehicle. The motors provide peak torque at their lowest RPM range and have a relatively low maximum RPM making them ideal for direct drive applications.
The motors are based on a dual radial gap architecture, This architecture is unique in that the motor has a donut shape. It features a rotor, with a channel shaped cross section that contains two separate opposing annular rings of magnets, each one attached to the two inside horizontal surfaces of the channel. The rotor is operationally attached to and rotates around a stator core centrally positioned within the two rotor magnet rings producing two separate additive radial torque components. This architecture demonstrates twice the power density of a conventional DC electric motor. It is essentially two motors in one, both an inside and outside rotor incorporated within the same machine. My motor also employs a unique modular architecture that simplifies its design, keeps initial tooling costs low and allows for full automated assembly.
This concept is ideally suited for converting fleet vehicles from IC to full electric power, as one kit can be designed for application to a number of similar vehicles within a fleet. Many fleet owners are currently looking for options on how to electrify their fleets and most have dedicated service centers where the installation of these kits could be easily performed.
For front wheel drive, the power-train consists of a compact dual motor system. Two dual electric motors, one for each wheel, will be mounted back-to-back in a cradle. It will be a direct drive application with no intermediate gear reduction units. The motors will be attached directly to the wheel hubs, by two constant velocity half shafts and individually controlled by two independent motor controllers whose power and torque would be coordinated by a central processing unit.
For rear wheel drive, one motor would be required. It would replace the engine and transmission and positioned for attachment to the existing vehicle prop-shaft.
Fleet operating efficiency would be improved. Electric motors are significantly more efficient than IC engines. They also benefit from the vehicle only requiring energy when it is in motion, therefore, there is no energy wasted due to motor idling when the vehicle is stopped. This concept also directly benefits the environment as there are no exhaust emissions. Other benefits include reduced maintenance and operating costs. The motors don’t use oil so oil changes aren’t required. These kits would replace much of the vehicle power-train components (engine, transmission, etc.), dramatically reducing vehicle complexity.
Kits could produced be by a fleet owner as a licensee or by my company (Lektromotiv, Inc.). Provisions could also be made for us to do the installation, should that be desired.
-
Awards
-
2020 Automotive/Transportation Honorable Mention
-
2020 Top 100 Entries
Like this entry?
-
About the Entrant
- Name:Bryan Prucher
- Type of entry:individual
- Software used for this entry:SpaceClaim 3D Modeling Software
- Patent status:patented