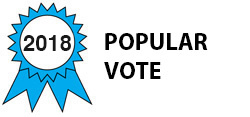
BrainE:
The focus here is the construction of a human free device (Robot) to operate on various surgical platforms so as to eliminate human errors, save time, reduce the chances of failures etc. and provide a leakage-free surgery to the patients. The project focused on automation of surgical tasks and reducing the time needed to perform teleoperated surgery beyond our planet.
The team has designed and build an autonomous robotic surgery system to overcome this communication issue and deal with relieving pressure in removing a blood clot. The team evaluated four design alternatives and chose the above multi-tool rotating end effector design approach because it scored highest in terms of tool change, the speed of operation and cost on a Design Alternative Matrix.
The surgical system the team has designed, built and tested is comprised of a mechanical and an electromechanical system.
On the mechanical side, we will have a servo motor with a mechanical encoder. The encoder will give feedback on traveling of the robot. Such as: when the spreader stretches the skin and particularly, stretches to a particular point, it stops after getting the signal upon completion.
Along with the spreader, there would be an end effector. Attached to the end effector are the cutting tools viz. the cutter- moving along the horizontal axis and the direction being controlled by the end effector it is used to cut the scalp and create an incision, the spreader mechanism enters the cut and pulls the skin back to expose the skull for drilling. The area of incision depends on the region where the clot is formed to relieve the pressure. Finally drilling tool- moving in the vertical axis and the movement is controlled by the end effector. The tool drills through the skull and relieves the blood pressure.
A small camera is also attached to the end effector to capture the images of the above operations and give a clear view of the process is carried out on external heavenly bodies.
The gearbox is another element of the system. It is used to change the speed and torque according to the load condition.
The electromechanical subsystem of the robot will be controlled using Arduino integrated microprocessor which will be programmed using C programming language. The microprocessor will communicate with the primary control computer using a serial connection. Primary control computer will be programmed using Python programing language due to its flexibility.
Spreading stage utilizes 2 stepper motors, which are driven by a single stepper driver. Stepper motors allow for precise positioning and position holding. The end effectors rotating arm is controlled by a servo motor. Servo motor is able to achieve high acceleration and velocity resulting in an increase of the robotic platform speed. The drill mechanism utilizes a geared DC motor. All of the motors utilize the same controller board which monitors the serial communications port for commands. Once the command is received, the microcontroller executes it with a confirmation response and other sensor data updates.
Video
-
Awards
-
2018 Top 10 Most Popular
Like this entry?
-
About the Entrant
- Name:Viraj Lele
- Type of entry:teamTeam members:Viraj Lele
Adomas Povilianskas
Shantanab Dinda
Mustafa Rifat
Zixuan Wan - Software used for this entry:Python,C++
- Patent status:pending