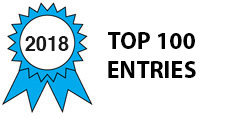
The Hyper4 (an axial 4 stroke, 4 cylinder engine) improves the fuel efficiency of internal combustion engines by up to 75% (as reflected by Simulink Matlab and Converge CFD modelling software), approaching 50% brake thermal efficiency in a unique, compact axial design that is both straightforward and inexpensive to manufacture. Unlike a standard inline engine, the incorporation of Constant Volume Combustion, Variable Compression ratios and Over expansion is virtually effortless. The configuration also allows for the inclusion of rotary valves and water injection for internal cooling and the reduction of NOx emissions. These fuel saving strategies are well known, researched and documented but are extremely difficult to implement in a conventional crankshaft controlled engine.
The cam tracks provide for the different piston stroke lengths and dwell at TDC and BDC. The cam assembly is movable along a splined output shaft to provide infinitely variable compression ratios during engine operation. The four cylinder engine provides four power strokes per output shaft revolution so power density is improved. For the major length of the power (expansion) stroke, the cam tracks apply the combustion’s pressure at 900 to the output shaft’s displacement arm minimizing the amount of energy absorbed by the block. Further, the counter-rotating cams will ensure that the con-rod and piston move in a strictly linear and reciprocal fashion minimizing vibration and piston side loads and therefore friction.
Water injection reduces both pumping losses and combustion temperatures which reduces NOx formation, without reducing power. The rotary valves (modified Bishop type) enhance volumetric efficiency while also providing for the throttle function and variable valve timing in one simple unit. The cams, cam followers and gear train are coated in a new very low friction, very high strength material (BAM) to reduce friction and wear and promote longevity.
Since this engine has twice the power strokes of a regular engine, and applies those strokes much more efficiently to the output shaft, compressed natural gas would be a suitable fuel. This would reduce the carbon footprint by 87.5% without affecting drive-ability. A larger unit (8 cylinders) using regular gasoline could replace the diesel engine eliminating soot and other emissions while still reducing the engine’s carbon footprint. The adjustable compression ratio would allow one to tune the engine for maximum efficiency for any given fuel, and the cams can be configured for maximum efficiency based on the individual application.
This engine may be utilized where any internal combustion engine is currently in place, but in particular the automotive and light truck marketplace which is about 88 million units, worldwide, per year. Another promising application is the use of the engine for the combined heat and power (CHP) production, particularly in domestic applications. We also see this engine’s early use as a range extender in hybrid vehicles since the integration engineering is minimal, and 75 mpg is achievable.
-
Awards
-
2018 Top 100 Entries
Like this entry?
-
About the Entrant
- Name:Bernie Bon
- Type of entry:teamTeam members:Bernie Bon
Jorge Martins
Francisco Brito - Software used for this entry:matlab, simulink, comsol
- Patent status:patented