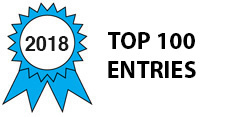
Slotted Waveguide Antennae Stiffened Structures (SWASS) aim to replace the large, bulky dishes and antennae used by aircraft with a waveguide structure integrated into the skin of the aircraft. Currently, antennae are mounted within large spaces inside the aircraft’s structure, creating large point loads that do not aid the overall aircraft’s strength, or externally, which negatively impacts the aircraft’s aerodynamic profile. SWASS panels aim to eliminate these and other issues by replacing the honeycomb structure within the skin of an aircraft with a slotted waveguide made of an electrically conductive material, such as copper, or a carbon-fiber reinforced plastic (CFRP). These panels are designed not only to perform the required antennae functions, but also to help bear the aircraft loads, thus aiming to reduce the overall weight of the aircraft. The panels operate by encasing the aforementioned conductive material in fiberglass and sandwiching it within the composite layers of current skin designs to maintain, or hopefully improve, their buckling and bending characteristics, while allowing for an electric current to be passed through the central waveguides and perform the necessary antennae functions.
Previously, similar designs were attempted with the F-35, but required the aircraft’s design to be modified to divert the loads away from the panels, increasing the overall weight of the aircraft. Therefore, the innovation of the SWASS design lies in its ability to bear the loads of the aircraft while retaining its functions as antennae with little to no weight increase. Such a design could be implemented in any number of aircraft with surfaces large enough to serve as the antennae being replaced. For example, with the recent growth of stealth technology, SWASS panels would allow for communications equipment to be integrated within the aircraft’s structure, eliminating the need for external antennae that could adversely affect its shaping and, thus, radar cross-section. The same could be said for potential supersonic aircraft, whose optimal shape may not leave enough internal areas to mount a proper antennae array.
Though currently still in the design phase, SWASS panel manufacturing would be relatively straightforward. The waveguide at the center could be sized and either cut from the appropriate metal, or laminated with carbon-fiber, in a uniform design, allowing for automated construction. Next, the slots would be cut into the top surface of the waveguide in a similar fashion. After the slots are cut out, the waveguides could be placed in a mold to be filled with a layer of fiberglass to add additional strength and, depending upon the buyer’s preference, bind the individual waveguides together into a single panel. Afterwards, this waveguide structure could be integrated into the current composite structure of a typical aircraft skin, with an additional fiberglass sheet above and a graphite-epoxy sheet below for additional strength. Since most of the manufacturing process could be automated, there would likely be little additional labor or cost in shifting the manufacture of current composite skin to one that integrates SWASS panels, increasing the design’s economic viability.
-
Awards
-
2018 Top 100 Entries
Like this entry?
-
About the Entrant
- Name:Joseph Brooks
- Type of entry:individual
- Software used for this entry:COMSOL Multiphysics
- Patent status:none