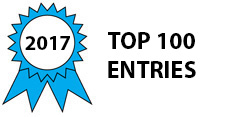
The printed electronics market is currently estimated at around US $20 billion and it is expected to grow up to about US $73 billion by 2025. One of the major driving factor of the global printed electronics market is “substrate,” on which electronic or photonic devices are integrated. Presently, hard-to-recycle substrates, such as glass and plastics, are widely common. On the other hand, so-called “nanosheets” made of cellulose fibers with nanometer size diameter, are emerging substrate candidates. 100% nanocellulose films are still quite expensive and in this configuration, the substrate can only be used in liquid-free environments or devices. Besides, the device performance coming from the light and ink interaction of the substrate remains restricted. Most common solution for these challenges is surface coatings.
Hybrid nanosheets are designed and realized in Aalto University, consisting of nanocellulose, a special recyclable filler polymer and catalyst. Depending on the specification of the application, new matrix can provide tailor-made substrates with desired (1) cost, (2) flexibility, (3) optical properties such as, haze, scattering and transmittance, (4) water/liquid repellence, (5) surface properties and (6) thermal characteristics without a surface coating. All these characteristics can be adjusted by the proportion of the cellulose, polymer and catalyst.
Main component of the hybrid nanosheets is the nanocellulose fibers, which act as a skeleton and the voids between the fibers are filled with an environmentally friendly polymer, changing the chemical and mechanical characteristics of the substrate. Finally, a catalyst is introduced to the system to tune the packing structure of the substrates by changing the ionic charge of the system. All the chemical reactions can be accomplished in an ordinary container by simply mixing the water-based dispersions, not necessarily in a clean room. The custom-made substrates can be easily produced using current lab technologies for proof-of-concept devices as well as available roll-to-roll manufacturing methods can be facilitated for mass production. Additionally, by only designing the substrate in advance according to the specifications of the application, the necessity of the coating step is eliminated.
Many applications can benefit from these bioplatforms such as point of care diagnostics, packaging systems and printed electronics. Additionally, due to its non-toxic nature, it can be employed in medical and biological applications, such as medical implants or skin patches. The films can also serve as membrane for battery applications since the porosity can be tailored. Moreover, introducing cellulose based substrates to the emerging energy technologies like third generation solar cells will accelerate their adoption into everyday life by consumers increasing the integration opportunities of the devices.
-
Awards
-
2017 Top 100 Entries
Like this entry?
-
About the Entrant
- Name:Merve Ozkan
- Type of entry:teamTeam members:Merve Özkan, Alp Karakoç, Maryam Borghei, Orlando J. Rojas and Jouni Paltakari
- Software used for this entry:Matematica
- Patent status:none