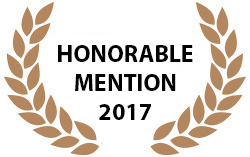
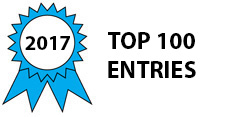
Currently all commercial continuously variable transmissions (CVT’s) in the automotive industry function on a friction drive principle. This friction drive interface exists between two hardened smooth steel surfaces separated by a traction fluid film. Traction fluid has the unique property in that it solidifies under high pressure, typically between 1 to 4 GPa, and then provides a traction coefficient of friction that varies from about 0.05 to 0.1. A number of factors determine the friction coefficient as well as the efficiency of the friction drive and as a result current commercial CVT’s do not feature high mechanical efficiencies, with a typical average mechanical efficiency of about 85%. Traction drive technology is a very well matured technology and has been in development since the 1980’s.
The RADIALcvt is a multi-parallel power path type of CVT that utilises traction drive technology in a novel mechanical configuration which optimise's the factors contributing to high mechanical efficiencies in traction drives. The following fundamental advantages sets the RADIALcvt apart from current CVT’s in the automotive industry to present the RADIALcvt as a cost effective, high mechanical efficiency CVT.
– One friction interface: Only one friction drive interface in series in a parallel power path. All other CVT’s, developmental and commercial have 2 friction drive interfaces in series thus resulting in a compound friction loss.
– Line contact: The friction drive contact in the RADIALcvt friction drive can be a line contact, which is only possible in belt/chain CVT and cone ring CVT and not possible in toroidal and planet ball CVT’s. Line contact reduces the maximum contact stress.
– Constant input radius: The RADIALcvt has a constant friction drive input radius. All other CVT have a variable input radius which results in high surface rolling speeds and lower coefficient of friction which require higher clamping forces.
– Six parallel power paths: The RADIALcvt has at least 6 parallel power paths. Such a large number of parallel paths is only possible in planet ball CVT’s.
– Large output friction disk: The output friction drive disk of the RADIALcvt can be positioned concentric and close to the engine flywheel and can approximate flywheel size. Thus the diameter of this output friction drive can be much larger than any of the belt/chain or toroidal or cone ring CVT output friction drive components. Due to this fact the RADIALcvt provides its highest efficiency in low ratios associated with city driving.
– High power efficiency: Above results in a RADIALcvt with a friction drive contact power efficiency in all ratios, under maximum engine torque, of about 95% in high ratio to about 98% in low .
– No hydraulic control: The RADIALcvt is realised without any hydraulic control. All current developmental and commercial CVT require a hydraulic control system which adds cost, weight and complexity.
The full simulation document of the RADIALcvt can be downloaded from http://www.varibox.com/media/1177/radialcvtdesignver16.pdf
RADIALcvt YouTube channel
https://www.youtube.com/user/Varibox
Overview
https://www.youtube.com/watch?v=7HSSdEkZKcY
Functioning mechanism 1
https://www.youtube.com/watch?v=Aww1OvBc32c
Functioning mechanism 2
https://www.youtube.com/watch?v=7885frPe7cw
Video
-
Awards
-
2017 Automotive/Transportation Honorable Mention
-
2017 Top 100 Entries
Like this entry?
-
About the Entrant
- Name:Jan Naude
- Type of entry:individual
- Software used for this entry:Solid Works, Matlab
- Patent status:patented