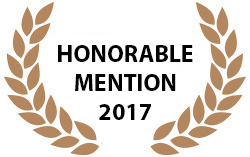
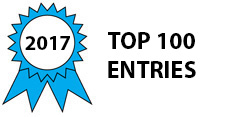
NASA's Langley Research Center has developed a new technique to enable the preparation of metal/composite hybrid laminates, also known as fiber metal laminates (FML), by depositing metal directly onto fabric using a plasma deposition process. FMLs provide a useful combination of structural and functional properties for both aerospace and non-aerospace applications. Currently, FMLs are prepared in a compression process utilizing a press or autoclave with metallic layers (foils) sandwiched between layers of glass or graphite prepreg (preimpregnated fibers with a matrix resin). The NASA process deposits the metal on the fiber via plasma deposition. The porosity of the coated fabric allows for resin infusion.
BENEFITS
Metal deposition directly onto fabric eliminates the need for separate foils and provides a better interlayer bonding
Porosity of coated fabric still allows for resin infusion and improved quality
Metal provides textured surface for improved matrix bonding
Variety of fabrics and metal alloys (e.g., aluminum, titanium, copper, glass fabric, carbon fabric, epoxy, polyimide) can be used to meet application requirements
Tailorable process with flexibility in terms of resin pathways (size, pattern) and finished parts (thickness, texture, permeability, single or multi-sided, etc.)
Final laminate products can vary in terms of stacking sequences, number of plies, metal/composite ratios, and fabric perform types
Program
Bringing NASA Technology Down to Earth
THE TECHNOLOGY
NASA's plasma-deposition process provides the ability to tailor various properties while designing functional parts by selecting specific materials and processing parameters to meet the end goal. Specifically, the plasma process deposits metal particles that are heated as they travel axially at low velocity through an inert gas plasma. The accelerated powder particles become molten, strike the substrate fabric (uniaxial, biaxial, and multiaxial) and rapidly solidify, imparting very little heat to the substrate while forming a metal-to-fiber bond, as well as a metal-to-metal bond. The resulting metal-coated fabric is porous, so the polymer matrix can pass through the product precursor during the infusion process. The amount of metal deposited can be controlled, as can the number of plies of fabric that are ultimately stacked to produce the preform for the polymer matrix infusion process. A variety of infusion processes can be utilized to prepare the FML, including resin transfer molding (RTM), resin film infusion (RFI), and vacuum-assisted resin transfer molding (VARTM). The tailorable aspect of the process allows for specific product design. By varying the combination of metal particle, fiber, fabric type, metal layer thickness, fabric direction, number of layers, polymer matrix resin, infusion process, and cure conditions, the characteristics of the final part can meet the needs of various applications.
APPLICATIONS
The technology has several potentialapplications:
• Aeronautics and aerospace - e.g., functional materials such as embedded lightning strike protection for aircraft, and structural applications such a fuselage skins, leading-edge wings, floors and liners, pressure bulkheads, landing gear doors, flap skins, and blast-resistant cargo containers
• Pressure vessels and storage tanks
• Ballistic protection
• Automotive structures
• Composite doors and windows
Patent No: 7,851,062; 8,017,190
-
Awards
-
2017 Automotive/Transportation Honorable Mention
-
2017 Top 100 Entries
Like this entry?
-
About the Entrant
- Name:Nasa Langley Research Center
- Type of entry:teamTeam members:Erik S. Weiser (NASA LaRC) Joel A. Alexa (Lockheed Martin) Roberto J. Cano (NASA LaRC) Brian J. Jensen (NASA LaRC) Stephen J. Hales (NASA LaRC)
- Patent status:patented