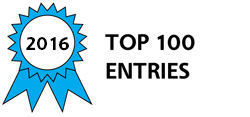
The Piston Deactivation Engine
For many decades it has been the desire of motor engineers to create a “flexible” engine with the ability to vary a number of parameters in order to achieve ultimate economy and/or ultimate performance. This flexibility is necessary to respond to the variable loads and conditions that are required by a vehicle to reduce fuel consumption. We have seen the introduction of many innovations, however, the “Holy Grail” of flexibility is Variable Capacity (VC) and to some degree, Variable Compression Ratio (VCR)
The Piston Deactivation Engine.
The Piston Deactivation Engine has been developed to allow complete flexibility in the quest to achieve maximum fuel economy in the way an engine is used in a vehicle. It is an innovative design that allows designated pistons to be stopped or “parked” when not required (unlike the cylinder deactivation engines where the pistons continue to be dragged within the cylinder). Not only do the active pistons operate at a higher efficiency, but the reduction in friction provided by the parked pistons, substantially increase fuel economy and reduce emissions. This is very much a fundamental requirement in the way an engine operates in a vehicle where partial loads are the norm.
A prototype 1.7 litre three cylinder Piston Deactivation Engine (PDE) has run successfully on one, two and three pistons. The principal of operation is demonstrated in the cross sections below:
Figure 1 shows the engine in the active position and comprises of a conventional crankshaft connected to the piston via a rocking adjustable four bar mechanism that has all pin jointed connections positioned on the opposite side of the cylinder relative to the crankshaft. The angular movement of the piston conrod is very small throughout the cycle almost eliminating the piston side force and hence friction.
By rotating the adjustor relative to the oscillator, the lower pin of the piston conrod is positioned to be concentric with rotational axis of the oscillator and the piston motion is reduced to zero while the closed oscillating mechanism remains in sync with the crankshaft at all times. Activation and deactivation can be achieved very quickly in response to vehicle demand with a helical spline actuator (not shown). See Fig 2.
This technology can be applied to a V6 engine to produces a 2-4-6 configuration as well as to diesel engines of all capacities.
The prototype three cylinder engine is a 1.7 liter capacity based on one half of a popular six cylinder engine and utilizes part of the cylinder block with pistons, and the complete head and part of the manifold. Effectively creating a multi capacity engine of 567cc, 1130cc and 1700cc. This is shown in Figure 3.
-
Awards
-
2016 Top 100 Entries
Like this entry?
-
About the Entrant
- Name:Joseph Scalzo
- Type of entry:individual
- Software used for this entry:Various solid modelling software.
- Patent status:patented