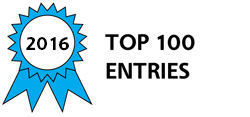
Currently there are over 1.25 billion units on the road (0.32 billion in the USA), a minimum of 5 billion brakes or 10 billion pads. In addition the industry manufactures around 90 million units per year which represents around 400 million brakes. All these deposit debris to the surroundings. The vehicle numbers represent the market potential for this design.
Dust is an environmental and health concern. The “Brake Pad Partnership” concluded that some 50% of brake dust becomes airborne and estimated that 580 tons of copper/year finds its way into California waterways - recommending “source control” rather than water treatment. European research estimates that brake wear will contribute up to 55% of non-exhaust air pollution from vehicles. The particle sizes less than 2.5nm penetrate deep into the lungs and international research concludes “the identified compounds are known to have adverse effects even with mutagenic and carcinogenic potency to humans.”
The proposal of “source control” has seen significant R&D devoted to copper free pads - significant time and money in order to satisfy this legislation demand. The alternative to “source control” is to “collect at source.”
No viable or cost effective on-vehicle dust collection system exists on the market. The Clean Brake Performance Module (CBPM), designed by Joe Gelb, is the only cost effective on-vehicle dust collection system that may be readily fitted to any vehicle. It embraces the entirety of the brake, has no moving parts and absorbs no power. Clean air flows into the disc vents and flows radially outwards. At the disc rim the module employs 2 lipped members to “tap-off” an amount of the airflow dictated by the degree of lip overhang into the vent outlet area. It is then directed into a bypass channel formed by the module outer casing to an outer high pressure region. The air then flows downwards to a low pressure region and back towards the disc surface where it “scrubs” the disc surface of dust as it is driven outwards to the rim of the disc. At this point a second lip guides the total airflow into a filter channel forcing it through the filters and back towards the disc surface. The air is thus constantly recycled and filtered. Once the recycling process has been established (whenever the wheel is rotating) the majority of air will pass through the disc vent so maximizing cooling.
Independent first prototype testing by LINK Engineering showed dust collection to be 92% by weight. In addition it was seen that disc thickness wear was reduced by 58%, inner pad by 17% and outer pad by 29%. It was also seen that over the majority of test cycles the brake temperature was reduced. The added advantage of a totally enclosed brake is that it reduces the effects of NVH as it inherently acts as a noise barrier.
The outer casing may be personalized to emphasize the character of the vehicle - constructed from carbon fiber, glass fiber, pressed brushed stainless steel or anodized aluminum alloy.
Video
-
Awards
-
2016 Top 100 Entries
Like this entry?
-
About the Entrant
- Name:Joe Gelb
- Type of entry:individual
- Software used for this entry:Creo
- Patent status:patented