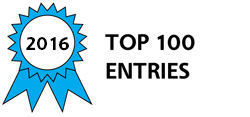
Technology:
The sensor system is an intelligent damage detection “skin” that can be embedded into structures, providing a lightweight capability for in-situ health monitoring for space or aircraft vehicles, inflatables, deployables, extravehicular activities (EVA) suits, smart wearables, and other applications where prognostic impact damage monitoring might be critical. The use of flexible printed circuitry or rigid circuitry in senor panel systems can be customized for detecting location, damage size, and depth, or designed for particular environments such as detecting space debris damage and additional flux data information in an International Space Environment (ISS) flight demonstration experiment.
The damage detection system and options for use of flexible printed circuitry designs along with current work into the integration of multiple non-rigid flexible printed components to increase the flexibility of the damage detection system could have game changing results. The reduction of rigid components in flexible printed circuitry and sensory damage detection systems for such applications as inflatable and deployable structures for NASA and commercial space exploration and for military applications could prove invaluable in the future.
Capabilities Provided:
The operation of the detection system is currently based on the use of parallel conductive traces placed on a firm or flexible surface making up the sensory panel/s system. Several detection layers can be implemented, where alternate layers are arranged in orthogonal direction with respect to the adjacent layers. The orthogonal arrangement allows for pinpointing the exact location of the damage or debris impact. Multiple detection layers will allow for the calculation of the depth of the debris impact or impact damage. Design options also include spacing options of the detection layers, graphical user interfaces (GUIs), and wireless communication for in-situ monitoring of the sensor system.
Benefits:
• Flexible individual detection layers in the structure or inflatable can be turned on or off to collect damage information as needed for a particular application. Embedded code can be modified to optimize system performance.
• Integrated flexible printed circuitry option for the intelligent sensor system with minimization of rigid components provides weight savings and enhances potential integration into inflatable/deployable architecture designs.
• Diagnostic information collected by the system would allow precise damage location and allow for repair activity initiation when needed to prevent catastrophic failure or to extend structural service life. Could significantly reduce life cycle cost and increase safety and structure/system reliability
• Addresses or enabling to technology gaps or needs identified by NASA for thermal and in-situ structural health monitoring for inflatables/deployable structures.
Applications:
• Inflatable and Deployable Structures
• Spacecraft
• Space Habitats
• Space Debris Monitoring
• Aircraft
• Military Shelters
• Solar Arrays
• Smart Garments and Wearables
• Extravehicular activity (EVA) suits
• Critical Hardware Enclosures
• Embedded Composite Structures
• Flexible Printed Electronics
Figure 1: Sensory panel design concept, controlled by a dedicated panel microprocessor, which communicates with a single board computer (SBC) controller. This particular design option is a potential flight experiment for detecting space debris in an International Space Station (ISS) environment.
-
Awards
-
2016 Top 100 Entries
Like this entry?
-
About the Entrant
- Name:Jeffrey Kohler
- Type of entry:individual
- Patent status:patented