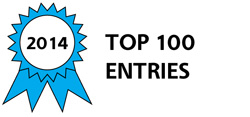
Magnesium is one of the most abundant elements on the Earth. Once made into an alloy, its applications can be just as numerous. From automobile parts to handheld device enclosures, magnesium can be an essential component to many of the products we use on a daily basis. Compared to aluminum and steel, automotive parts made with magnesium alloys are lighter, burn less fuel, and ultimately release less carbon dioxide into the atmosphere.
Unfortunately, the current methods for extracting magnesium require high energy consumption. There are two main methods used for extracting magnesium. As shown in Figure 1, both methods require a high reduction temperature and a large amount of energy. In terms of waste production, one of the methods (the Pidgeon Process) releases a significant amount of carbon dioxide.
The processes currently used are costly and can have negative impacts on our environment. We were inspired to develop a process for extracting magnesium that is both economical and environmentally friendly. Our process can be performed at room temperature and thus saves energy. It also uses easily attainable raw materials and produces zero carbon dioxide within the extraction stage.
As seen in Figure 2, our process uses membrane electrodialysis. In the cell, aqueous MgCl2 is pumped into compartment M at m1, providing the Mg2+ and Cl- ions for the reaction. Depleted MgCl2 exits compartment M at m2 to be recycled.
The anolyte is pumped into compartment A at a1. An electrical potential difference is applied, and negatively charged Cl- ions migrate through the anion exchange membrane toward the positively charged anode. Cl- ions are oxidized at the anode to become Cl atoms. Two Cl atoms combined with H2O molecules form wet Cl2. This gas leaves compartment A at a2 and is captured as a byproduct.
In compartment C, the non-aqueous, organic catholyte is pumped in at c1. Positively charged Mg2+ ions migrate through the cation exchange membrane toward the negatively charged cathode. Mg2+ ions are reduced at the cathode to become Mg atoms (powder). The catholyte is pumped out at c2, and enters a solid-liquid separator which removes the Mg powder from the catholyte. The catholyte is then recycled back to c1 and the Mg powder is collected.
Magnesium powder obtained through this new process has many applications. It can be directly used as a desulphurizing agent for steel mills. It can also be used as hydro-reactive metal fuel for water ramjet engines. In addition, it can be melted with other elements to produce magnesium based alloys. The United States Automotive Materials Partnership predicts in the report supported by the Department of Energy, “Magnesium Vision 2020: A North American Automotive Strategic Vision for Magnesium”, that passenger cars made in the U.S. may increase from 10-12 lbs. to 350 lbs. of magnesium alloy per car by the year 2020.
Success in the laboratory has been promising. Further improvements will allow us to carry this process into the commercial stage.
-
Awards
-
2014 Top 100 Entries
Like this entry?
-
About the Entrant
- Name:Wuliang (frank) Zhang
- Type of entry:teamTeam members:Teresa Zhang
- Patent status:pending