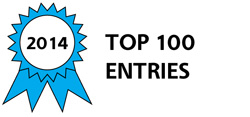
Using the highly articulated All-Terrain Hex-Limbed Extra-Terrestrial Explorer (ATHLETE) robotic mobility system as a precision positioning tool, a variety of print head technologies can be used to 3D print large-scale in-situ structures on Earth and other planetary surfaces such as the moon or Mars. In effect, in the same way CAD models can be printed in a 3D printer, large-scale structures such as walls, vaults, domes, berms, paving, trench walls, and other in-situ derived elements can be FAXed to the planetary surface and built in advance of the arrival of crews, supplementing equipment and materials brought from prepared sources.
The ATHLETE is a six-limbed wheel-on-limb robotic mobility platform that is capable of transporting large cargo efficiently on both rolling and rough terrain. The fundamental premise of the ATHLETE system is that for sufficiently large systems, by designing the wheels and wheel actuators for relatively benign terrain, the system saves enough mass to offset the mass of the robotic limbs. A key feature of this design, exploited by FACS, is that these limbs can serve as general-purpose robotic manipulators. ATHLETE is able to mitigate the risk of a stuck wheel by simply locking the affected wheels and walking out of the troubling terrain or stepping over the obstacle. In this way the multipurpose robotic limbs are not only part of the mobility system, but are able to be used as capable manipulator arms as well. The addition of a tool adapter with an interface to a power takeoff shaft eliminates the need for individually powered end effectors. Various functional versions of ATHLETE prototypes have been operational since 2006.
The FACS system, built upon the ATHLETE mobility platform, will function as an onsite robotic construction tool that does not require the presence of human operators, but can alternatively function at the direction of onsite human crews. The FACS system is an additive manufacturing system that is capable of "3D printing" large-scale walls, paving, vaults, domes, and hardening trench walls. The FACS printing system could be used on Earth, the moon, Mars, or other planetary surfaces, creating compressive structures via melting and bonding loose native material found on the site. Five ATHLETE limbs will be available for mobility, while the sixth limb will be devoted to tool manipulation. Material reservoirs, filters, crushers, processors, sorters, and mixers will be installed on the pallet, with a material handling system that delivers processed material to a printhead manipulated by the sixth limb. The mobility system situates the platform in an accessible location, whereupon the ATHLETE limb positions the printhead to build up in-situ structures in a layered fashion.
Four technologies have been explored for potential application to a FACS 3D additive manufacturing printing process, (1) microwave sintering "sinterator", processing and melting in-situ soil that is found locally onsite; (2) fiberoptic solar concentrator, also processing and melting in-situ soil; (3) single-part in-situ derived concrete, laying a slurry that will harden in place; and (4) multi-part binder agent using in-situ aggregate.
-
Awards
-
2014 Top 100 Entries
Like this entry?
-
About the Entrant
- Name:A. Scott Howe
- Type of entry:teamTeam members:Scott Howe
Brian Wilcox
Chris McQuin
Julie Townsend
Richard Rieber
Martin Barmatz - Software used for this entry:SolidWorks, Form-Z
- Patent status:pending