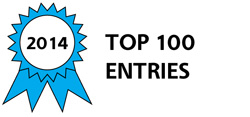
Atlas Motors and New Frontier Technology Group are developing several rotary devices optimally suited for propulsion (engine), pumping (hydraulics), or gas compression/expansion (pneumatics).
One result of the development will be the realization of the Ducted Blade Rotary Engine (DBRE). Along with offering a potent combination of power and economy, the DBRE will not exhibit noise, vibration or harshness associated with conventional engines. DBRE's innate balance and simplicity will ensure that the cost of its design, manufacturing and ownership will be less than that of a conventional engine.
How It Works:
The DBR is designed with a rotating disc that is sandwiched between two plates. These plates contain a series of small chambers/cylinders. The rotating disc itself carries spinning drive plates, each of which contains a lobe/piston. The individual lobes/pistons in turn engage each of the chambers/cylinders sequentially. With each sweep of a lobe/piston through a chamber, a complete exchange of gases occurs. Air is drawn in behind one sweeping drive plate while exhaust gases are pushed out in front of that plate. The four Brayton cycles (as in a turbine), are positively displaced and separately processed for optimization. Consequently, the aerodynamic penalty at partial power with turbines is eliminated and the engine can operate at any speed even >20,000 rpm making it most suitable for electric-hybrid vehicles/aircraft. In an alternate embodiment the air-gas mixture is completely burned in a central combustion chamber and expanded fully in the expansion chambers/cylinders.
This operation and functionality gives the DBR remarkable power density. A 525 cu in, 400hp engine can be only about the size of a moped/scooter tire.
DBR Efficiency
1) The power output is continuously variable. For conventional engines power is constant relative to the RPM. When driving at a constant speed, a conventional engine will produce a specific amount of power, and consume a specific amount of fuel, irrespective of whether it is needed or not. On the other hand, the DBRE’s output can change on the fly to meet specific power demands. The power output can change from 40 to 400HP in a split second!
This is accomplished by varying the packets of air and fuel. As the packets get smaller, lesser horse power is produced but the burn efficiency is higher. Excessive compression is not built up, but instead an “ultra lean” condition is achieved. An additional advantage of this ultra lean mix is lower combustion temperature and NOX emissions.
2) Conventional engines suffer from ‘pumping loss’ because the pistons are working against themselves and is the primary reason why engines must waste fuel idling. By dynamically metering the power stroke gases, the DBRE is fed with just the requisite amount of fuel which eliminates the so-called pumping loss. Fuel can be metered down to a pilot flame or even stopped. Once stopped, the DBR can be turned by releasing high-pressure air from an accumulator. There is no need to idle and waste fuel while stationary in traffic. Full power is available from zero RPM.
4) Further efficiencies are possible.
-
Awards
-
2014 Top 100 Entries
Like this entry?
-
About the Entrant
- Name:Milan Krupa
- Type of entry:teamTeam members:Milan Krupa
John Robitaile - Patent status:patented