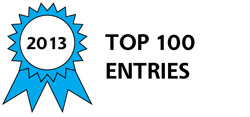
Today’s challenge in robotics is the same that it has always been: to apply original technology to a task. With more than two million of such machines in use worldwide, can a single innovative American design mean that significant expansion will be forthcoming?
The answer to that question is now a resounding YES.
By offering a new approach to part handling, the Two Roll Gripper solves the mystery behind applying robotics to greater task challenges, and promises to revolutionize the industry.
By creating the Two Roll Gripper, Michigan research and development engineer Larry Phillips focused on increased efficiency and profitability. His lightweight design delivers the answer for a practical alternative to expensive robotic upgrades and ongoing remodeling. It also is capable of providing a wide variety of applications.
The long-term success of robotic maneuverability is connected to an adaptable blueprint and the arrangement of effectors. Ordinary two- and three-fingered grippers clasp parts and twist at the “wrist,” while the Two Roll Gripper offers more innovation and pliancy.
Its purpose is to provide robotic arms with versatility by securely holding and arbitrarily moving a grasped object. By adding another axis of movement perpendicular to wrist motion, the robot also establishes work performance at the end of the arm, in a process called leveling motion.
The Two Roll Gripper approaches handling with a parallel-jawed twin track apparatus, unlike other effectors, because it simulates the rolling action between human fingertips and the thumb, and can level motion. This occurs by incorporating the movement of two tracks that seize, lodge and guide parts to a designated attitude and location.
When the Two Roll Gripper zeroes in on its target, a scanner is activated to measure the distance to the tool’s center, putting the grip and track in motion. As that clasp approaches the part, it is drawn between the tracks through a combination of friction, submissive built-in springs, and track mobility. This compresses the springs, eventually triggering switches connected to the DC motors and actuators that open and close the jaws.
That places the part between the tracks and returns the springs to their home position where it nests. Motion is leveled by part rotation in the grippers with rotation in a perpendicular attitude to wrist movement; that rotation occurs by the tracks running in opposing directions at the same speed.
Two gear-reduced DC motors attached to linear actuators regulate the grippers’ opening and closing through adjustable slip clutches that control the clenching force; two more encoded motors engage and master the track motion. The end effector can be closed-loop, and by using the encoded track and jaw position feedback, will control and operate the tracks.
With many end effectors already in operation, the Two Roll Gripper provides the harbinger of new direction for global robotic flexibility. This new approach could well spur engineers to develop a new generation of applications in all industries and services.
-
Awards
-
2013 Top 100 Entries
Like this entry?
-
About the Entrant
- Name:Larry Phillips
- Type of entry:individual
- Patent status:none